Manufacturing processes play a pivotal role in transforming raw materials into finished goods, shaping the products we use and rely on in our daily lives. From automobiles to electronics, clothing to food, virtually every product undergoes a series of manufacturing steps before reaching consumers. In this article, we delve into the intricacies of manufacturing processes, exploring their significance, key components, and impact on industries and economies worldwide.
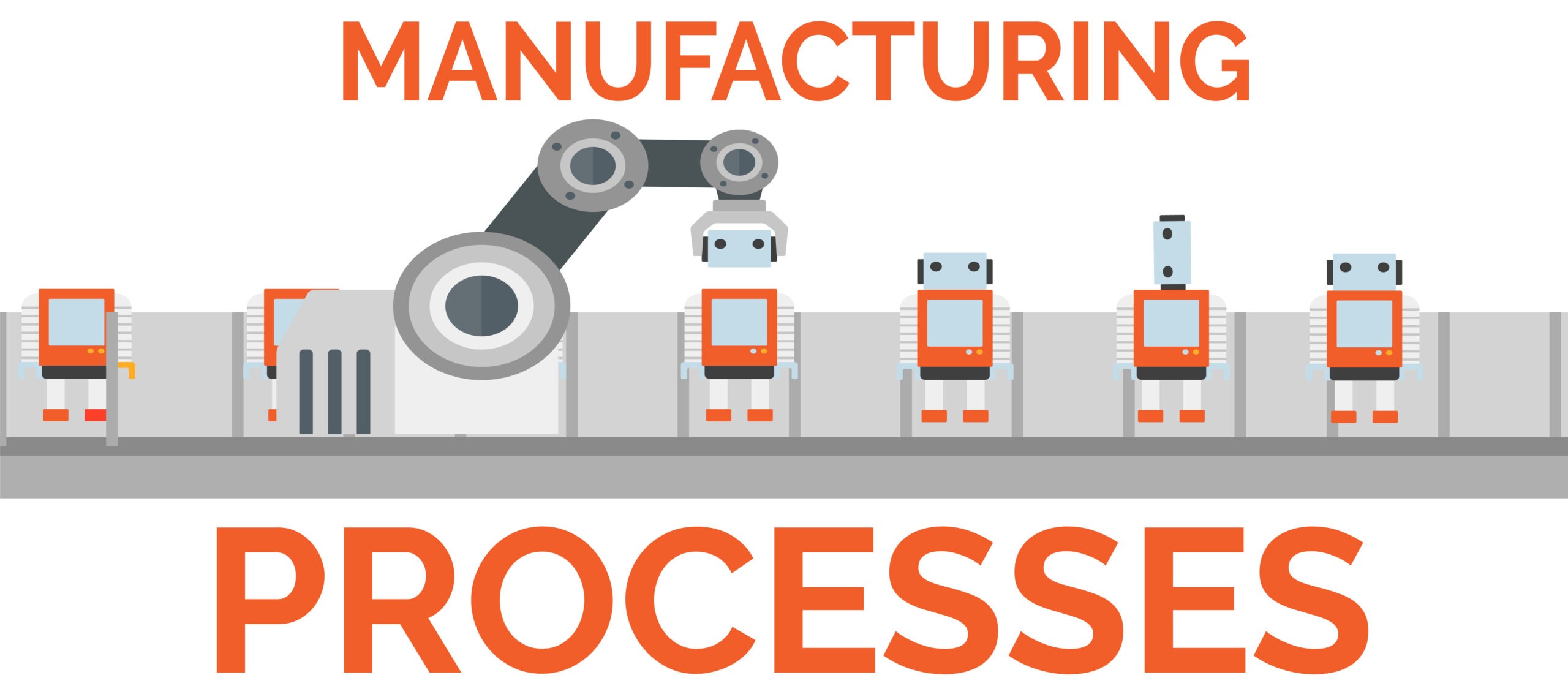
1. Introduction to Manufacturing Processes:
Contents
- 0.1 1. Introduction to Manufacturing Processes:
- 0.2 2. Types of Manufacturing Processes:
- 0.3 3. Key Components of Manufacturing Processes:
- 0.4 4. Impact of Manufacturing Processes:
- 1 Pros and Cons of Manufacturing Processes: Balancing Efficiency and Challenges
- 2 Best Practices in Manufacturing Processes: Ensuring Efficiency, Quality, and Sustainability
- 2.1 1. Comprehensive Planning and Design:
- 2.2 2. Standardization and Documentation:
- 2.3 3. Lean Manufacturing Principles:
- 2.4 4. Automation and Technology Integration:
- 2.5 5. Quality Assurance and Control:
- 2.6 6. Supply Chain Management and Collaboration:
- 2.7 7. Environmental Sustainability and Responsibility:
- 2.8 8. Continuous Improvement and Innovation:
- 2.9 Conclusion:
- 3 Author
Manufacturing processes encompass a broad range of activities involved in the production of goods, including design, fabrication, assembly, and quality control. These processes can vary significantly depending on the nature of the product, industry standards, and technological advancements.
2. Types of Manufacturing Processes:
There are several types of manufacturing processes, each tailored to specific product requirements and production goals. Common types include:
- Forming Processes: Such as casting, molding, and forging, involve shaping materials into desired forms through the application of heat, pressure, or mechanical force.
- Machining Processes: Such as milling, turning, and drilling, involve the removal of material from a workpiece to achieve the desired shape, size, and surface finish.
- Joining Processes: Such as welding, soldering, and adhesive bonding, involve combining multiple components or materials to create a cohesive product.
- Additive Manufacturing: Also known as 3D printing, involves building objects layer by layer using digital design files and additive techniques.
3. Key Components of Manufacturing Processes:
Manufacturing processes typically consist of several key components, including:
- Raw Materials: The basic materials used in production, such as metals, plastics, textiles, and chemicals.
Equipment and Machinery: Tools, machines, and equipment used to manipulate, shape, and assemble raw materials into finished products.
Labor and Workforce: Skilled workers and technicians responsible for operating machinery, monitoring production processes, and ensuring product quality. - Quality Control Measures: Inspection, testing, and quality assurance protocols implemented to maintain product standards and consistency.
Supply Chain Management: Coordination of suppliers, logistics, and distribution channels to ensure timely delivery of raw materials and components.
4. Impact of Manufacturing Processes:
Manufacturing processes have far-reaching implications for industries, economies, and societies worldwide. Some key impacts include:
- Economic Growth: Manufacturing contributes to economic growth by generating employment, driving innovation, and fostering industrial development.
- Global Trade: International trade relies heavily on manufactured goods, with manufacturing processes serving as a cornerstone of global supply chains and trade networks.
- Environmental Sustainability: Sustainable manufacturing practices aim to minimize resource consumption, waste generation, and environmental impact through the adoption of eco-friendly technologies and processes.
- Product Innovation: Advances in manufacturing processes drive product innovation, enabling the development of new materials, technologies, and consumer products.
Manufacturing processes are the backbone of modern industry, shaping the products we use and rely on in our daily lives. By understanding the intricacies of manufacturing and their impact on industries and economies, we can appreciate the vital role they play in driving innovation, economic growth, and societal progress.
Pros and Cons of Manufacturing Processes: Balancing Efficiency and Challenges
Manufacturing processes form the backbone of modern industry, enabling the mass production of goods that drive economies and shape societies. However, like any system, manufacturing processes have their advantages and disadvantages. In this article, we explore the pros and cons of manufacturing processes, highlighting the benefits they offer and the challenges they present to industries and societies worldwide.
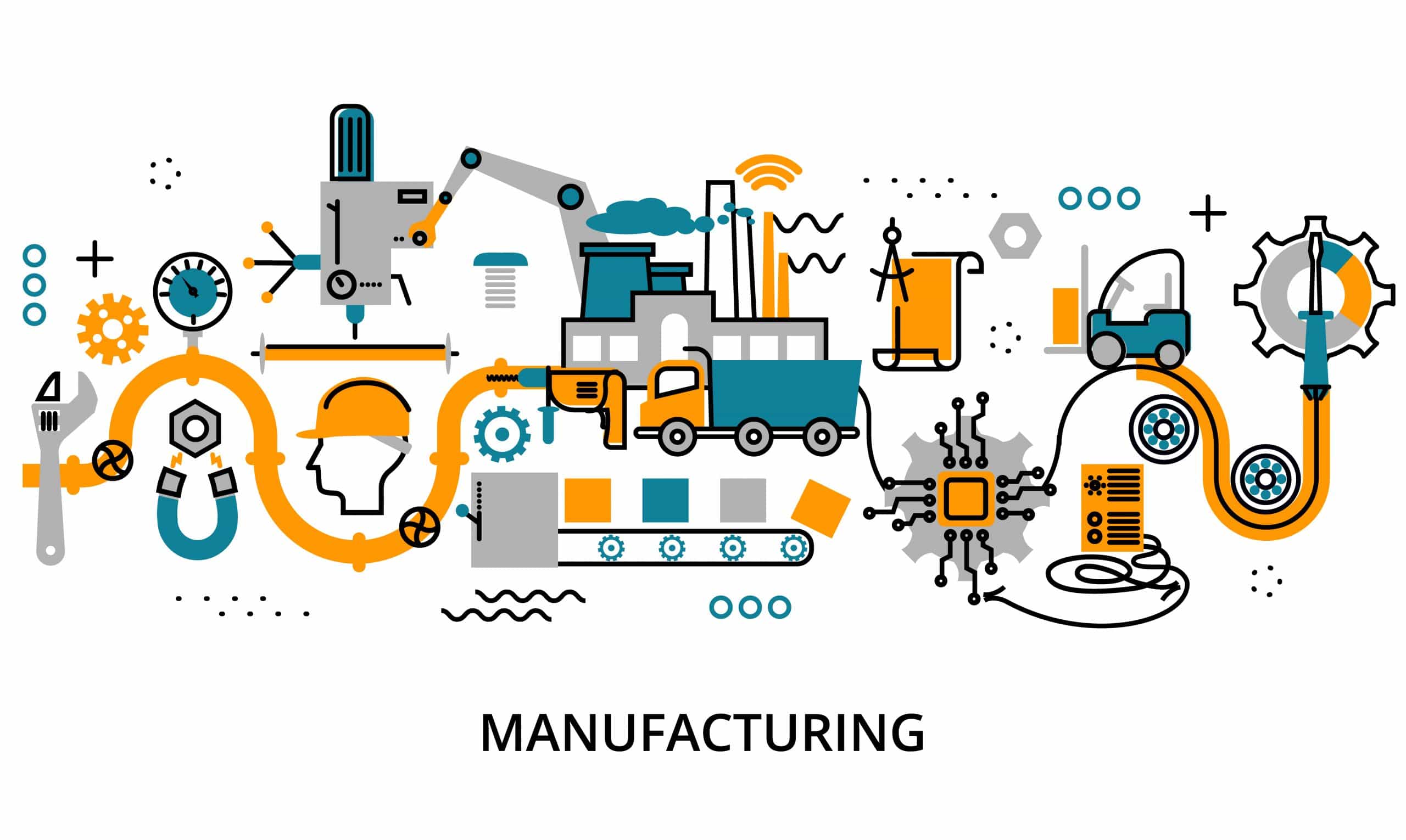
Advantages of Manufacturing Processes:
- Efficiency: Manufacturing processes streamline production, allowing for efficient and cost-effective mass production of goods. Automation, mechanization, and standardized procedures contribute to increased productivity and reduced labor costs.
- Consistency and Quality Control: Manufacturing processes employ rigorous quality control measures to ensure consistency and product quality. From raw material inspection to final product testing, quality assurance protocols help maintain standards and meet customer expectations.
- Economies of Scale: Mass production enables economies of scale, allowing manufacturers to produce large quantities of goods at lower per-unit costs. This cost efficiency can lead to competitive pricing, increased market share, and higher profitability.
- Innovation and Technological Advancements: Manufacturing processes drive innovation and technological advancements, fostering the development of new materials, processes, and products. Advances in automation, additive manufacturing, and digital technologies enhance efficiency, precision, and customization capabilities.
- Job Creation and Economic Growth: Manufacturing processes create employment opportunities and contribute to economic growth by supporting a diverse workforce, supply chain networks, and ancillary industries. Manufacturing hubs serve as economic engines, driving investment, infrastructure development, and regional prosperity.
Disadvantages of Manufacturing Processes:
- Environmental Impact: Manufacturing processes can have significant environmental consequences, including pollution, resource depletion, and habitat destruction. Energy consumption, waste generation, and emissions contribute to environmental degradation and climate change, necessitating sustainable practices and regulatory compliance.
- Supply Chain Vulnerabilities: Globalized supply chains are susceptible to disruptions, such as natural disasters, geopolitical tensions, and supply chain bottlenecks. Dependencies on international trade, just-in-time inventory management, and single-source suppliers can exacerbate supply chain vulnerabilities and lead to supply shortages or disruptions.
- Labor Displacement and Automation: Automation and mechanization in manufacturing processes can lead to labor displacement and job loss, particularly for low-skilled workers. The shift towards automation raises concerns about unemployment, income inequality, and the social impact of technological advancements.
- Product Standardization and Homogenization: Mass production often prioritizes efficiency and cost reduction over product customization and diversity. Standardized manufacturing processes may lead to product homogenization, limiting consumer choice and innovation in favor of mass-market appeal.
- Regulatory Compliance and Compliance Costs: Manufacturers must comply with various regulations, standards, and industry requirements governing safety, environmental protection, and product quality. Regulatory compliance entails administrative burdens, compliance costs, and legal liabilities that can impact profitability and operational efficiency.
Manufacturing processes offer numerous advantages in terms of efficiency,
Quality control, and economic growth, but they also present challenges related to environmental impact, supply chain vulnerabilities, and labor displacement. By addressing these challenges through sustainable practices, technological innovation, and stakeholder collaboration, manufacturers can maximize the benefits of manufacturing processes while minimizing their adverse effects on society and the environment.
Best Practices in Manufacturing Processes: Ensuring Efficiency, Quality, and Sustainability
Manufacturing processes serve as the cornerstone of industrial production, enabling the transformation of raw materials into finished goods efficiently and effectively. To optimize manufacturing operations and achieve desired outcomes, it is essential to adhere to best practices that promote efficiency, quality, and sustainability throughout the production process. In this article, we explore the key principles and guidelines for implementing effective manufacturing processes.
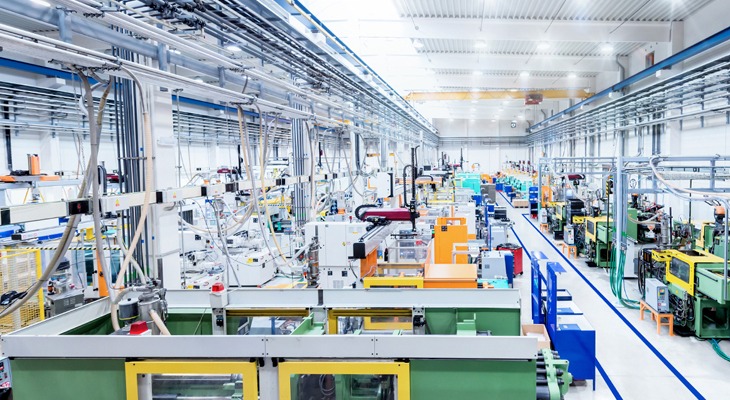
1. Comprehensive Planning and Design:
Successful manufacturing processes begin with thorough planning and design. Define clear objectives, specifications, and requirements for the product or components being manufactured. Develop detailed production plans, workflows, and timelines to guide operations and ensure alignment with organizational goals.
2. Standardization and Documentation:
Standardize manufacturing procedures, processes, and specifications to promote consistency, repeatability, and quality assurance. Document standard operating procedures (SOPs), work instructions, and quality control protocols to provide guidance to operators and facilitate training, troubleshooting, and continuous improvement efforts.
3. Lean Manufacturing Principles:
Adopt lean manufacturing principles to eliminate waste, streamline workflows, and optimize resource utilization. Implement techniques such as value stream mapping, 5S (Sort, Set in order, Shine, Standardize, Sustain), and Kaizen (continuous improvement) to identify inefficiencies, reduce cycle times, and enhance productivity.
4. Automation and Technology Integration:
Leverage automation, robotics, and digital technologies to enhance manufacturing efficiency, accuracy, and scalability. Integrate advanced manufacturing technologies such as computer-aided design (CAD), computer-aided manufacturing (CAM), and industrial Internet of Things (IIoT) to enable real-time monitoring, data analytics, and predictive maintenance.
5. Quality Assurance and Control:
Prioritize quality assurance and control throughout the manufacturing process hometogel to ensure that products meet or exceed customer expectations and regulatory requirements. Implement quality management systems (QMS), statistical process control (SPC), and inspection procedures to monitor product quality, identify defects, and implement corrective actions.
6. Supply Chain Management and Collaboration:
Establish robust supply chain management practices to optimize procurement, inventory management, and supplier relationships. Foster collaboration and communication with suppliers, vendors, and subcontractors to ensure timely delivery of materials, components, and services while minimizing supply chain risks and disruptions.
7. Environmental Sustainability and Responsibility:
Promote environmental sustainability and corporate social responsibility (CSR) by integrating sustainable practices into manufacturing processes. Minimize energy consumption, waste generation, and emissions through resource-efficient production methods, waste reduction strategies, and renewable energy adoption. Comply with environmental regulations and standards to mitigate environmental impact and promote sustainable development.
8. Continuous Improvement and Innovation:
Cultivate a culture of continuous improvement and innovation within the organization to drive operational excellence and competitive advantage. Encourage employee involvement, creativity, and problem-solving skills to identify opportunities for improvement, implement process innovations, and adapt to changing market demands.
Conclusion:
Effective manufacturing are essential for achieving operational excellence, product quality, and sustainability in today’s competitive marketplace. By adhering to best practices in planning, standardization, automation, quality assurance, and continuous improvement, manufacturers can optimize their processes, maximize efficiency, and deliver value to customers while minimizing environmental impact and promoting social responsibility.
Read More Article About “BLUEFIN TUNA DISH TEMPTATION: SAVOR THE DELIGHTS OF THIS EXQUISITE DISH“